Boldrocchi: Italia
Boldrocchi Italia tailor-makes each solution based on your parameters and needs and provides in-house design, manufacturing, testing, installation and commissioning to customers in a wide variety of industries. We specialize in fans, blowers, compressors, heat exchangers, coolers, gas turbine systems & noise protection, heavy-duty process dampers and air pollution control/environmental solutions. We not only provide in-house testing, but on-site testing by qualified and experienced Boldrocchi employees.
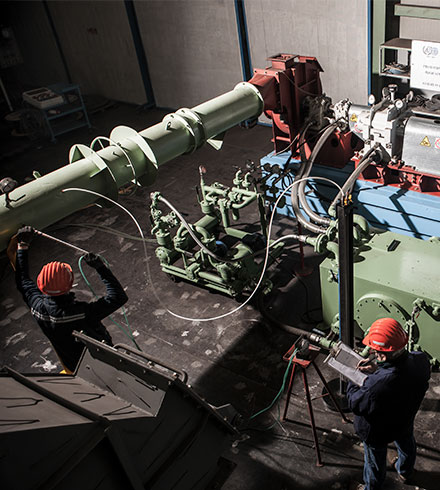
In-House Manufacturing in Italy
Boldrocchi Italia prides itself on offering customers from a wide array of industries a truly turnkey experience. The company has invested in its manufacturing and testing facilities, as well as in its engineering, technical and service departments to ensure clients receive reliable, well-conceived and well-made systems. We not only provide in-house testing, but on-site testing by qualified and experienced Boldrocchi employees.
Our manufacturing facilities include:
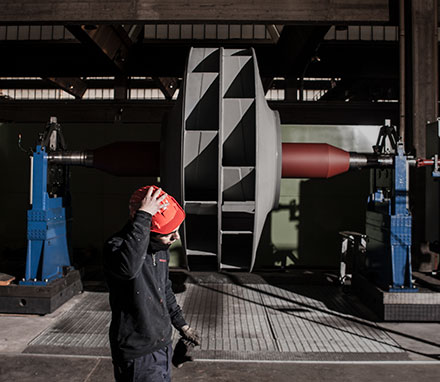
Balancing machines up to 44 tons
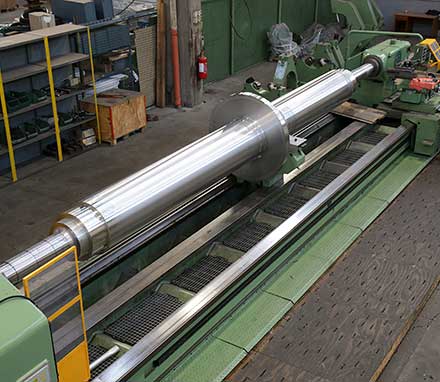
Shaft machining up to 12 m (30 tons)
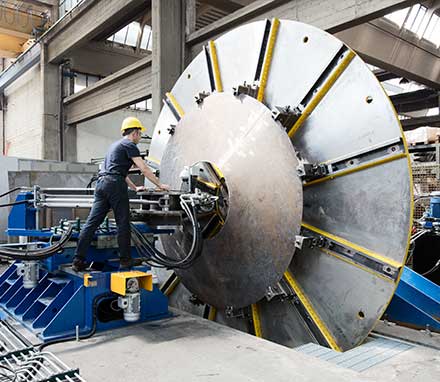
4.2 m spinning machine
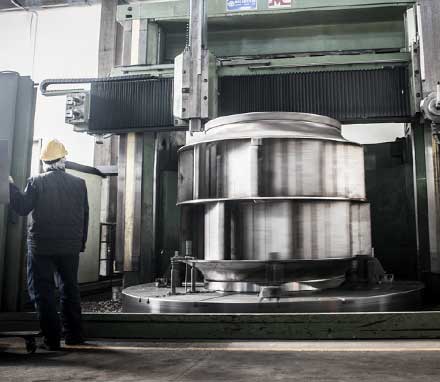
Rotor balancing up to 4.2 m diameter
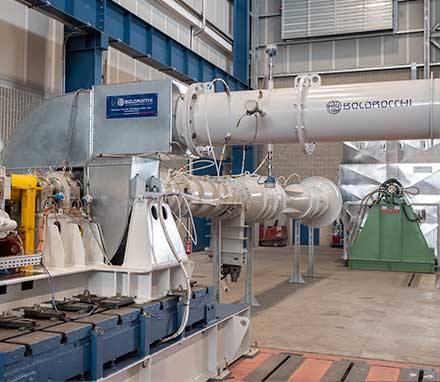
11 finning machines
(footed fins, embedded, extruded)
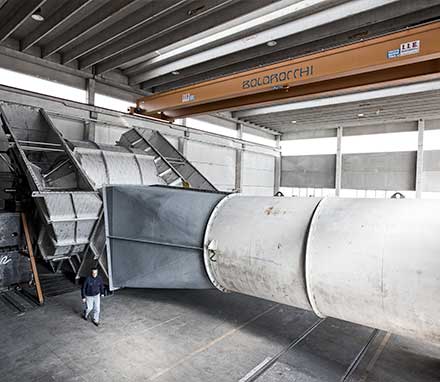
Running test for fans & heat exchangers
In-House Testing in Italy
- 3 test rooms with installed power of up to 2.5 MVA (~2.0MW@motor axis)
- Voltages from 380V to 13.8kV
- Medium voltage VFD with output frequency of 5-140Hz
- Fan testing capacity of up to 8MW (at no load and full speed)
- Performance tests as per AMCA 210, ISO 5801, ASME-PTC10, ASME-PTC11
- Mechanical running tests and overspeed tests as per API 673, API 560, API 672, API 617
- Hot gas test of up to 600°C
- Non-destructive testing (NDT)
- Acoustic compliance tests
- ASME & PED hydrostatic tests
- Bags and cartridges performance test rig
- Hydraulic test of up to 680 barg
- Thermal tests of up to 300 kW for transformer oil-air coolers (ODAF-OFAF)
- More than 500 PQR
- 70-ton mobile crane for outdoor activities
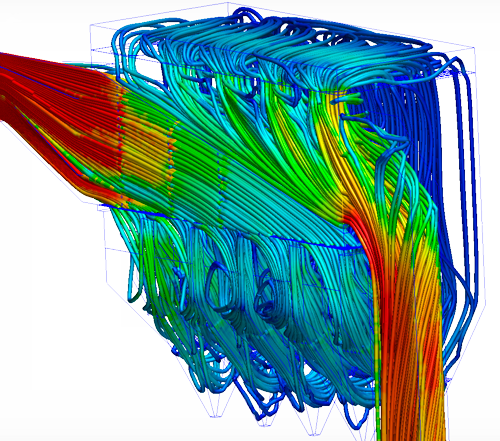
Boldrocchi Italia develops its solutions using some of the most trusted techniques in the industry:
- Finite element analysis (FEA), frequency analysis and computational fluid dynamics (CFD) studies
- State-of-the-art software for material selection
- Manufacturing using the latest techniques:
- Rolled and profiled inlet cone and shroud using spinning operation
- Machining of the impeller to limit axial & radial play
- Integral hub shaft forging
- Qualified welding procedures and welders
- Strict quality control
- Performance verification in shop and/or site
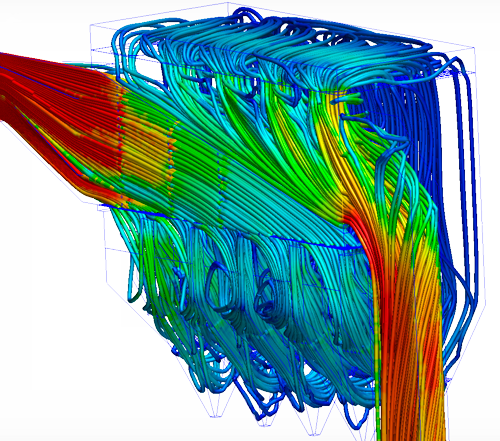